What are the four properties of knife steel, and how can they be used to evaluate a quality knife? Let's make some sense out of the 'what is the best blade steel' madness.
Edge Retention (also called Wear Resistance)
The first property is edge retention. The better the edge retention, the less sharpening will need to be done after repeated use. The principal reason that steel alloy is used as a knife blade metal system is edge retention. This property is a measure of how well the knife holds an edge and is due to the carbide formation of the steel mixture. Carbides are formed in steel due to the addition of various elements to the iron matrix base: carbon, chromium, molybdenum, tungsten, and vanadium. Carbon is the basic and key element in carbide formation. Carbides vary in types, hardness, and quantity in different steel alloys, with vanadium carbides being the hardest and smallest carbide; thereby producing the best edge retention. While not provided by most knife makers on a knife-to-knife basis, an industry-standard to rate edge retention is the CATRA (Cutlery Allied Trades Research Association) test.
Toughness
Toughness is the second property. It is a measure of how well a knife will handle a striking impact without chipping, breaking or cracking. Unfortunately, as the hardness goes up, the knife tends to become more brittle and edge (the thinnest part of a knife) could break or chip more easily - even at the microscopic level. Finding the ideal balance of edge retention and toughness is key to good all-purpose steel. Some steels that excel at toughness may not be very good edge retention. If you are going to use your knife blade with extreme chopping force, extreme environments and on very hard materials, the toughness of the steel becomes a very important feature of the knife.
Corrosion Resistance
The third property is corrosion resistance, which measures how unlikely the steel is to rust. The addition of chromium in a steel alloy makes a knife blade less likely to rust over a while. Although all stainless steels can rust under extreme situations of prolonged exposure to salt or water, steel alloys, above 12% chromium alloy are considered 'stainless'. The higher the amount of chromium in steel alloy, the higher-rated resistance to rusting over a longer time. You can normally obtain the amount of chromium percentage in a data chart for the steel.
Hardness
The final knife steel property is hardness, which is achieved through a heat-treating procedure. Knife blades are fabricated in a softened, pre-heat treated state, once the shape and grinding of the blade is complete, heat-treating provides the knifemaker the final hardness of the steel. Heat treatment realigns the alloy's elements, hardens the steel's matrix and provides the cutting properties of steel. Selecting the heat treatment of a knife steel blade is done by the knife maker and impacts both edge retention and toughness. Heat treating level is measured in Rockwell Hardness C (HRC) and will provide a direct measurement of the hardness level of the steel blade. Selecting a hardness number is a balancing act of providing optimal edge retention, toughness and takes into consideration the intended use of a blade. Most Rockwell Hardness levels you see in high-end knives fall between 58 and 62 HRC.
Now that the four properties of knife steel are known, it is possible to go out and make a more informed purchase of a knife. Knife Art has a wide selection of knives which demonstrate the four properties and will make an excellent first knife or addition to a collection.
Other factors to consider outside of the direct scope of the steel are the blade geometry, blade length, blade coatings, blade finishes and much much more...
Four Properties of Knife Steel
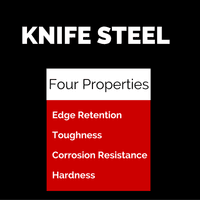